パナソニックの#はたらくってなんだろう
半導体の進化を追求する、超高精度の実装設備を開発
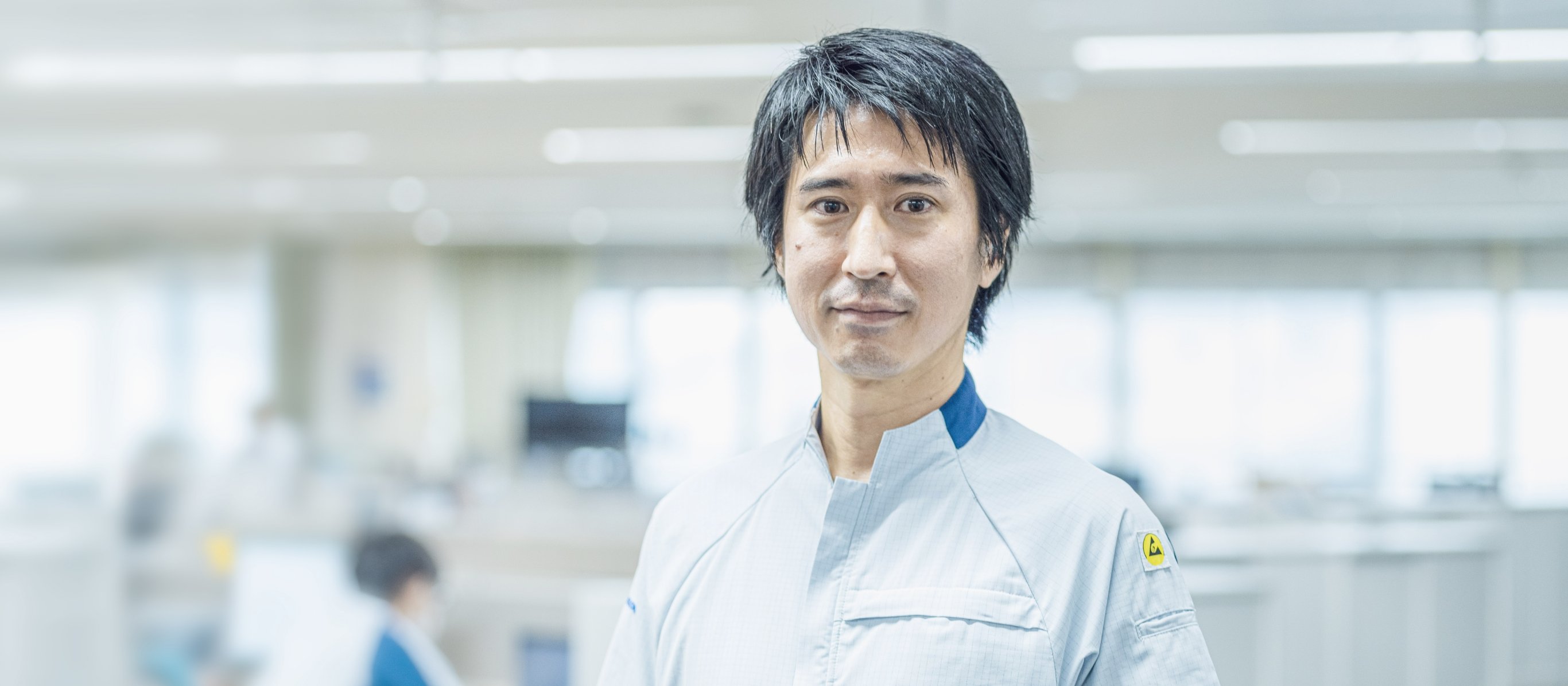
あらゆる電子機器、さらに機器を製造する設備に組み込まれて「心臓」の役割を果たす半導体。5G、AIを活用したデジタル化の加速で需要が一層急拡大し、半導体なくしてあらゆる電子機器は成り立たないと言っても過言ではありません。その半導体製造を下支えするのが藤田さんの専門分野です。超高精度が求められる実装設備の開発において、従来のメカ設計の枠を超えた幅広い技術力で、品質と生産効率の向上に貢献してきました。実装設備開発の進化と、ハードからソフトまで知識を押し広げてきた歩みについて聞きました。
プロフィール
-
藤田 亮
パナソニック ホールディングス株式会社 技術部門
マニュファクチャリングイノベーション本部 高度生産システム開発センター
先行設備開発部大学在籍時に機械工学と光計測、プログラミング技術を修め2004年に入社。ハードからソフトまで設備開発に必要な技術を併せ持ち、多面的な判断力で半導体実装設備の高精度化や電池向け積層設備の工程短縮などの事業化に貢献。現在担当している次世代半導体の実装設備では、業界最高性能レベルの高精度技術を目指して開発をけん引している。
目次
Mind_01知識を広げ、多面的に見る
半導体の実装設備ではどのような技術を開発しているのですか?
実装設備とは、電子回路の基板上にチップなどの電子部品を自動装着し、半導体を製造する設備です。近年、スマートフォンやパソコンなど電子機器を中心に高速化、小型化が加速し、これらの機器に実装される半導体の性能も進化が求められています。従来の単一電子部品の微細化では性能向上の限界があるため、新たな高性能化の手法として、機能の異なる複数の電子部品を組み合わせて一つのサブ基板に高密度に搭載し、高機能な一つの部品(パッケージ)とする手法が主流になっています。微細な電子部品を高密度で基板に装着するには、これまで以上に実装設備の高精度化が必須となります。
現在、私たちのプロジェクトチームが開発している次世代半導体向けの実装設備は、こうした高密度基板の微細実装を実現するため、業界最高レベルのサブミクロン、1万分の1ミリの精度向上を目指して研究を積み重ねています。このサブミクロンよりも10倍大きいミクロンサイズでも、装着した部品の位置ずれを計測することが難しく、仮にずれていてもどの機器に原因があるのか、手探りで解明するほかありません。
開発当初、部品を位置決めする精度がなかなか向上せず、基板に部品を装着するヘッド部分の振動に原因があると考え、改良を重ねていたのですが、思うような結果が出ない。そんなとき、そもそもヘッドではなく、部品を認識している光学系がぶれているのではと、疑問が浮かび、調べてみるとその通りでした。位置決めの際には、部品の位置をカメラで撮像・認識して、それを元に補正移動するのですが、その補正の元になる部品認識位置自体が温度変化などの影響でわずかにズレていたのです。
藤田さんは、なぜ高精度化のキーポイントをいち早く発見できたのでしょうか?
位置決め精度に関わる要因を考えるにあたり、複数分野にわたってさまざまな要因を考えることができたからだと思います。通常、専門分野の技術者はそれぞれの範疇で要因などを考えます。認識光学系を担当する人は光学系の問題である収差や画像処理アルゴリズムによる影響などを考えるのが得意な人が多いですが、熱ひずみなどはメカ設計の人の方が得意です。私はその両方をイメージできるので、今回のような光学系自体の熱影響という問題に対して解決の糸口をつかむことができたのだと思います。
私はメカ設計を基軸にしているのですが、学生時代に光学、プログラミング、入社後すぐにCAE*と呼ばれるコンピューター上で設備強度などを計算する設計技術を習得していました。幅広い知識を駆使して多面的に判断できるのが私の強みだと思っています。専門分野の技術者には知識の量や「深さ」では及びませんが、抱えている分野の数、「広さ」という観点では設備技術者の中でも自負があります。多岐にわたる技術知識が必要な設備開発において、常に別角度からアプローチできるメリットは大きいと言えます。
*CAE(Computer Aided Engineering):高品質な設備開発を行うためのコンピューターを活用した設計技術。3次元の図面上で設備の強度などをシミュレーションで予測ができる。
別角度からのアプローチで工期短縮を実現
自身の強みである多面的な判断力は、半導体以外の設備開発でどう生かしていますか?
積層電池の設備開発を担当していた時、プログラミング技術を生かしてカムを設計し、工程短縮化に成功しました。カムとは運動の方向と大きさを変え、精細で正確に動作する機械要素で、通常は複数ある定型パターンから理想の動作に近いカムを選び、形状の微調整を繰り返しながら完成させることが多いのですが、新たに開発する積層電池の設備では極めて複雑な動作が求められたため、定型にないカム曲線をゼロから設計しなければなりませんでした。
図面を一から描き起こして実物を作っていては、到底工期に間に合わない。そこで、プログラミング技術を活用し、数学的アプローチから理想の動作に合致したカム形状を計算できるオリジナルソフトを自ら開発して、導き出した数値をもとに実際にカムを作り、理想通りの動作を実現できました。従来、ソフト技術者とメカ技術者の2人でカム設計ソフトを制作した場合、ソフト技術者はカムの制約が分からず、メカ技術者はどうすればソフトを楽に組めるか分からない。私は双方を理解できていたので、良いところ取りができた結果、手戻りもなく、短期間で開発ができました。
Mind_02学び続けて個性を磨く
ハードとソフト、複数の技術を身に付けるために心掛けていることは?
子どものころからモノづくりが好きだったこともあり、大学では機械を専攻。学部4年では光学を用いた生体計測を主とした研究室に配属されました。光学関係はこの時に触れたのですが、大学院では制御関係も身に付けたく、ロボット制御の研究室に移り、ソフトウエア技術が主体に。画像処理関係もこの時に習得しました。入社後は設備の機構設計・開発の部門に配属され、そこではメカ設計に加え、学生時代とは畑違いのCAEを初めて学ぶことに。
入社から数年がたち、設備1台を構想から任せてもらえるようになってから、ばらばらだと思っていたこれらの技術が設備開発という一点で全てつながっている、そこに気づきました。これは大きな発見であり、喜びでした。「たとえ今が理想と違っても学ぶ姿勢を続けていれば、いつか必ず役立つのだ」と。今回、私が高度専門職に選ばれたのは、ハードとソフト両面の技術を生かした実装設備開発への貢献が評価されたからです。学び続けることは自身の活動範囲を広げ、他の技術者とは違う個性を磨き、強みにもなりうる。そういった信念を持ってさえいれば、どんなときも前向きに技術習得が行えるのではないでしょうか。
パナソニック ホールディングスは、取り扱う商材が多岐にわたるため、関連技術も幅広い。知識、視野を広げるという意味において、2012年から約2年間、社内の生産技術部門に所属した経験も私にとって貴重でした。これまでの開発部門とは真逆の立場に立ち、初めて発見できたことが多かったからです。実際に作業している社員の姿を目の当たりにして、お客さま視点のものづくりの大切さを改めて胸に刻みました。
視点を変えれば、マイナスもプラスになる
開発で壁にぶつかったとき、どのような考え方で臨んでいるのでしょうか?
たとえ失敗しても別の経験に生かせられないか、常に前向きに考えるようにしています。設備の使用条件や使用可能な部品からくる制約などさまざまな条件からどうしても不利なアプローチを選ばざるを得ないときがありますが、そんな時は、逆にその不利な部分を生かす手段はないかと冷静に思い直すようにしています。マイナスも角度を変えればプラスに転じる。あらゆる選択肢に可能性が秘められているのではないかと、前例や従来の枠組みから疑ってみる。そのためにも専門外の分野まで幅広く枝葉を広げて技術を吸収し続けられるよう、心がけています。
To the Next
次世代半導体であらゆる製品に貢献を。
当面の目標は、現在開発中の次世代半導体の実装設備を市場に送り出し、世界でどこまで通用するか見てみたい。半導体はスマートフォンやパソコンをはじめ、ロボットを制御する電子機器などに搭載されており、いわば「根っこ」のような存在。私たちが開発を進める次世代半導体の実装設備は、より小型で性能に優れた半導体製造を目指していますので、電子機器の高性能化だけでなく省エネや低コストなどさまざまな付加価値を与えられるのではと、期待しています。世界最高レベルの精度は必ず達成させる。さらに開発・製造現場だけでなく産業界の需要やニーズを随時取り入れながら、精度はもちろん、それ以外のアピールポイントも積み重ねて、さまざまな技術の調和がとれた厚みのある設備に仕上げていきたいです。
*所属・内容等は取材当時のものです。