パナソニックの#はたらくってなんだろう
「ナノの穴」で感度が10倍に!世界中のパートナーと挑んだ温度検知の革新で未来が変わる。〜熱型 赤外線センサセル 開発プロジェクトチーム インタビュー〜
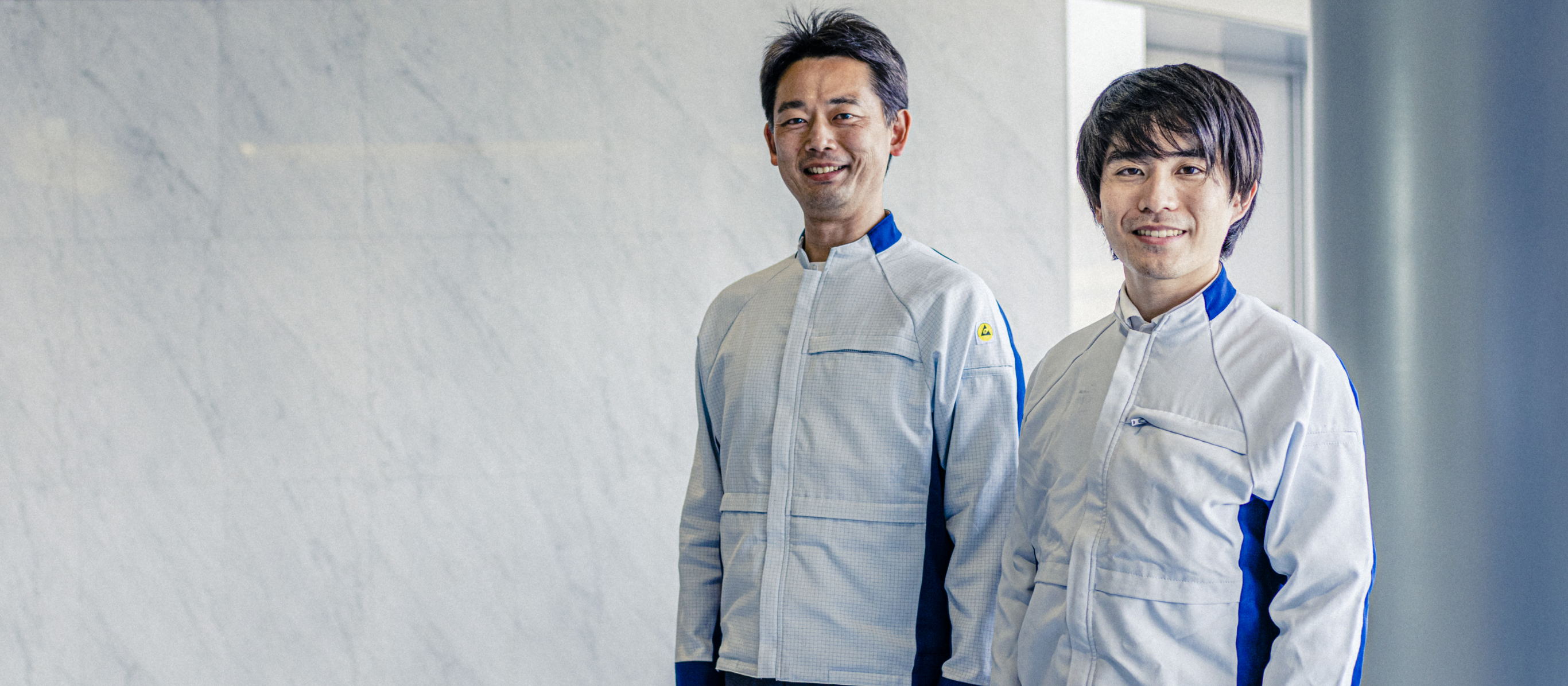
感度10倍化を実現する高断熱フォノニック結晶搭載熱型 赤外線センサセルの開発
体温検知機器への搭載など、熱型赤外線センサはすでに私たちにとって身近なものになっています。さらに、空間での熱(温度)分布の把握によって省エネや快適性向上を実現したり、夜間の安全運転をサポートしたりするなど、広く社会を支えています。性能を向上させれば、さらなるお役立ちにつながるはず。こうした思いを胸に、社会の革新をめざしてセンサを高精度化する技術開発に挑んだプロジェクトチームに話を聞きました。
プロフィール
-
反保 尚基
パナソニック ホールディングス株式会社
-
高橋 宏平
パナソニック ホールディングス株式会社
-
中村 邦彦
パナソニック ホールディングス株式会社
-
姫野 敦史
パナソニック ホールディングス株式会社
-
藤金 正樹
パナソニック ホールディングス株式会社
目次
PROBLEM
熱型赤外線センサのボトルネックを超える
人体や物体が発するわずかな赤外線を検知する熱型赤外線センサ。温度分布を描き出すことで、例えばエアコンでは人の居場所を検知して最適な風を届けるなど、より暮らしやすい環境づくりに活かされています。
検知精度の鍵をにぎるのはセンサ素子の内部にある受光部です。受光部は本体基板から支柱を介して宙に持ち上げられた構造をしており、受け取った遠赤外線を熱として吸収します。しかし、この支柱を通して基板などに受光部の熱が漏れ出してしまうため、測定の精度に悪影響を及ぼすことが課題でした。
今回開発に挑んだ技術は、支持部に「熱を遮断する(通さなくする)ためのしくみ」を組み入れて、受光部から熱を漏れないようにして検知精度アップをめざすもの。その熱を打ち消すしくみが、「フォノニック結晶」というナノメートルオーダーの穴です。
INTERVIEW
光でできるなら熱でも。世界的な難題に挑む
センサの感度10倍を実現する新技術、その原理とは?
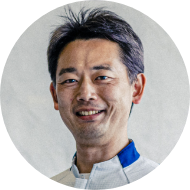
さらに、物理的な制約もありました。従来の研究では電子線によって材料に穴を開けていますが、直径50~100ナノメートル程度までしか穴を小さくできず、限界があります。そのレベルではフォノンを効果的にコントロールすることはでません。素材が準備できなければ、当然研究も進まない。そんなナノの世界が、2010年くらいから変わり始めました。知見が少しずつ積み上がり、世界中で興味を持つ研究者が増え、この10年でナノスケールでの熱制御は注目分野になりました。

テスト材料を準備して、高橋さんが2016年にフォノニック結晶の原理実証に成功。その年に、パナソニックが本格的に取り組み始めました。私は2017年に入社してすぐにこのプロジェクト配属に。大学時代にはレーザー冷却をテーマとしており、極めて緻密に光を扱う必要のある研究をしていましたが、くしくも高橋さんも光学が専門。そんな2人が異分野とも言える熱に挑む、運命のようなものを感じました(笑)。
電子線でも難しい小さな穴を、どうやってつくるのですか?

私たちは「自己組織化リソグラフィ」という技術を使って、材料に穴を開けています。光や電子線を使ったリソグラフィが一般的ですが、直径50ナノメートル以下の穴を自在に開けることは困難です。そこで、私たちは自然の力を利用した材料加工をめざしました。
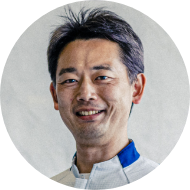
水と油のように相反する性質を併せ持つブロック共重合体(BCP)というポリマーをウェハに塗布すると、材料の配合に合わせた形状が自然とでき上がる「自己組織化」が起こります。自己組織的にでき上がったパターンを素材に転写するので、自己組織化リソグラフィと呼びます。所望の構造が、分子の自発的な整列でウェハ全面に形成される点が最大の特徴です。

電子線で穴一つひとつを照射するのはコスト的にも合いませんが、この方法は低コストの量産にも期待が持てそうでした。
「原子の振動を手中に」。人類が熱を操る時代の幕開け
開発を行う上で、1番の課題は何でしたか?

原理は実証されているものの、実用化するには実際の材料でどこまでの性能を引き出せるかを知らなくてはなりません。穴のサイズ、穴同士の距離間など、それぞれが変わるとどのように性能が変化するのか。最適なパラメーターは一からの手探りでした。
自分たちだけでは完結できないと考え、各分野のプロに協力を仰ぎました。自己組織化を用いた材料作製は、最先端技術を持つ海外の大学に依頼。入社したばかりの私は期待を胸にテスト材料を心待ちにしましたが、最初の材料づくりはつまずきの連続でした。きれいな穴ができない。穴が上手に並んでくれない。
解決するにはつぶさに加工条件を詰めていくしかありませんでした。レシピひとつで穴の形状が変わるという性質は技術の展開性の高さを意味する一方で、私たちが求める均等な間隔を持つ穴にするには、極めてシビアな調整が求められます。新規開発の難しさに直面しました。
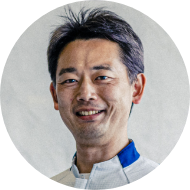
私は2018年に異動してきて、以来プロジェクトリーダーを務めています。海外から届く材料は少しずつ良くなったものの、私たちの求めるクオリティーをなかなか満たせずいました。そこで先方の大学に飛んで、作製現場を見学することに。きれいな研究棟に広い実験室、最新鋭のクリーンルームや充実した実験装置群、さらには学生やスタッフの多さにまず驚き、研究費の違いをまざまざと見せつけられました。
現場でさらに驚いたのが、作製作業にあたっていただいている学生同士の意見の食い違いから研究が進んでいなかったこと。試作を依頼している共同研究者の立場として見過ごすことはできず、私も議論に加わり最適な進め方を共に模索しました。日本からのオンラインのやりとりではまるで分からず、現場に触れる大切さについて身をもって知りました。そこからはネゴシエーションの毎日です。自分たちの行いたいことをするには何が必要で、どんな装置や熟練者が求められるか、とにかく粘り強く交渉を重ねました。世界を相手にするのはこういうことかと思い知らされました。

材料以外にも、問題は山積していました。ナノレベルの熱を測定する術がない。数千万円するような熱の測定機器も世の中にはありますが、独自試作のナノ構造について熱を測れるような汎用品は存在しません。結局は自分の手で装置を築き上げるしかありませんでした。
そこから測定器の開発も同時にスタートしました。ナノレベルの熱を測るというのは、それだけ小さな世界で起こる現象をじっと観察しないといけないということ。ここで生きたのが大学時代の専門性でした。従来は電気の力(エレクトロニクス)で測定を試みていましたが、私はレーザー冷却で培ってきた精密な光制御技術を用いてアプローチしました。
心掛けたのはシンプルな設計です。レーザー光線がぐらついては、ナノの世界で起こる小さな変化を見逃してしまうため精度が出ません。ネジやアジャスターを増やせば取り回しはよくなりますが、求められる精度が桁違いなので余計なものはなくそうと判断しました。初代の測定器完成は2017年のこと。これまで試作してきたさまざまな材料やデバイス構造に対して実験・検証を繰り返し、毎年改善を重ねて今では4代目に。用途に合わせてさまざまな測定ができるようになってきており、今後も開発の加速や新しい現象の発見に活躍することを期待しています。
こうした独自の測定器をつくり上げたからこそ、誰にも見えなかったことを明らかにすることができました。微細構造によってフォノンの波が打ち消し合うと言われていましたが、穴と穴の間隔をある距離にした時に、熱の伝わりが極めて小さくなることが確かに分かり、これまでの性能を凌駕する断熱性能を見いだしました。これには感動しました。後は、さまざまな組み合わせを当たり、最適解を導き出すのみ。2019年のある日、感度10倍に迫る、かつてない実験結果が飛び込んできました。
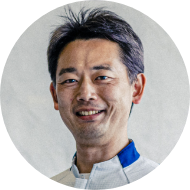
あの日のことはよく覚えています。その報告を見て、これが世に出たらえらいことになると思いました。思わず反保さんに、「このデータを発表するともう後には戻れないが大丈夫か」と問い掛けたほどです(笑)。

結果に驚くよりも先に、「本当かな?」という思いが頭をよぎりました。ただ、これは多くの新規開発を行った先人たちがたどってきた道だと思います。さまざまな証拠(実験データ)をかき集めて、その結果が確かと分かった時は達成感でいっぱいでした。
要素技術の原理検証を達成した今、実用化に向けて開発を続けております。「欲しい」という引き合いは多くとも、実際にセンサを商品化できなければ話になりません。研究開発部門の我々にはモノづくりのノウハウがなく、社内外の協力を得ながらどのように量産を実現するかが次の課題です。
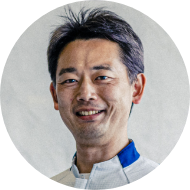
ベルギーの研究機関imecと連携して実用化を模索しており、最適なパートナー探しに奔走しています。技術には絶対の自信を持っているので、社会に貢献するキーデバイスに育てていきたいです。
MESSAGE

国内外のさまざまな大学・研究機関との連携による材料作製や断熱メカニズム解明などいろいろな協力を得て、ついに「ミクロの熱」を見える化・制御できました。今までの常識は「熱の物性を変えられるわけがない」。受光部をつなぐ支持部を細くして影響を少なくする方法が一般的でしたが、加工限界があるために行き詰まりを見せていました。ある構造を組み入れるだけで感度アップをめざす発想は世界から驚きをもって受け止められており、国際学会から招待講演に招かれるなど注目を集めています。
大きな一歩ではありますが、まだ「学者から好評」の域を出ていません。熱の困りごとは多いため高感度センサの可能性は無限大ですが、一方で現場によって悩みの種類が全く異なる特徴も。コンセプト自体には一定の評価をいただけているものの、センサの実物を示した上で具体的な議論をすることなしには実用化は進んでいかず、開発の難しさを実感しています。熱のプロフェッショナルとして、その答えを模索していきます。
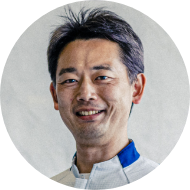
私はもともと固体物理学をやっていましたが、フォノニック結晶については驚かされることばかりでした。確かに理論は分かりますが、実際に物性評価をしてみるともっとおもしろい。私が目を付けたのは弾性率で、これは材料の硬さを示します。ある穴と他の穴の薄肉部位(ネック)が100ナノメートルを切ると、材料固有の弾性率が下がり、柔らかくなるほどに熱を伝えにくいことが分かりました。この技術は応用の可能性に満ちており、「熱」に関わる現場を知ることで、さらなる使われ方も開けるのではないでしょうか。
日本は新しい物理現象の発見を得意としており、それを産業につなげることを連綿と続けてきました。そこに求められるのは、物性の基礎の基礎からしっかり理解した技術者に他なりません。パナソニックにはもっとマニアックなオタクが多くていいはずですし、今後材料デバイス分野の後輩を鍛えていきたいと思っています。
FUTURE
熱型赤外線センサセルは今、需要の高まりとともに世界中で開発競争が進められています。スマートファクトリーやBEMS(ビルエネルギーマネジメントシステム)など、空間ソリューションの分野ではすでになくてはならない存在です。自動運転への期待が高まる車載分野においても注目度は高く、高精度な空間検知で車載に多く利用されるLiDARは夜間や悪天候下で性能を発揮できませんが、熱型赤外線センサはそれを補完する存在として認知されており、すでに世界中の自動車メーカーが導入を進めています。
また、日本において有力視されるのがインフラモニタリングの分野。道路やトンネル、橋といったインフラの老朽化はまったなしの社会問題ですが、現在は人の手で打音検査して安全性を確認しており、膨大な作業工数とコストがのしかかっています。この感度10倍のセンサセルがあれば、従来のセンサでは捉えることができなかったクラックや水漏れによって生じる躯体内部のわずかな温度変化でさえも確実にキャッチ。監視工数の大幅削減につながります。ドローンに搭載すれば点検困難場所の検査などにも役立ち、次世代の検査ソリューションとして活躍が見込まれます。
写真左から高橋 宏平(ベルギーimec駐在)、反保 尚基、藤金 正樹、姫野 敦史、中村 邦彦、田中 浩之
<関連リンク>
遠赤外線センサの感度向上技術を開発
「バイオナノプロセスによる電子デバイス作製の展望」
*パナソニック・先端技術研究所(当時)における"自己組織化"の研究事例
*記事の内容は取材当時のものです。
まず、「熱」が原子の振動、すなわち「波」として伝わっていくことを理解してください。この振動、熱の媒体をフォノン(Phonon)と呼びます。ボールが壁にぶつかれば跳ね返りますが、波も同じように反射します。ここで、波の周期(波長)と同じ間隔で配置された物体に波が押し寄せると、それぞれの物体から反射された波がちょうど重なり合う「干渉」や「回折」と呼ばれる現象が起こることが知られています。フォノンも波であるならば、その波長の大きさの構造を用意することで、熱の伝わり方を人為的にコントールできるのでは。そんな仮説が、そもそもの出発点です。干渉や回折効果を駆使し、受光部で吸収した熱が漏れ出ないようにコントロールしてセンサの感度を高めるというのが、私たちの基本的なコンセプトです。
このプロジェクトを起案した高橋 宏平さんは、「テラヘルツ」という周波数の光を研究する光学の専門家です。光の分野では、ナノ加工技術を用いて光を閉じ込めて制御するフォトニック結晶(Photon=光)という特殊な構造があり、それを熱に応用したフォノニック結晶という技術をパナソニックで実用化したい、という発想に至りました。
もっとも「光でできるなら熱でも」となるのは自然な考えの流れで、フォノニック結晶の発想は過去にも世界中でありましたが、産業利用まで実現した例はありません。その原因は、光に比べて熱の波長はとても短く、おまけにその長さもバラバラなためです。レーザー光線などは1色のため狙ってコントロールできますが、熱はさまざまな色の光がいろいろな方向に混ざり合っているようなものなので、まとめてコントロールしづらかったのです。