パナソニックの#はたらくってなんだろう
生産性向上、加工精度アップ 拡大する車載市場で存在感を放つ~顧客ニーズを捉えた設備、工法進化への挑戦~
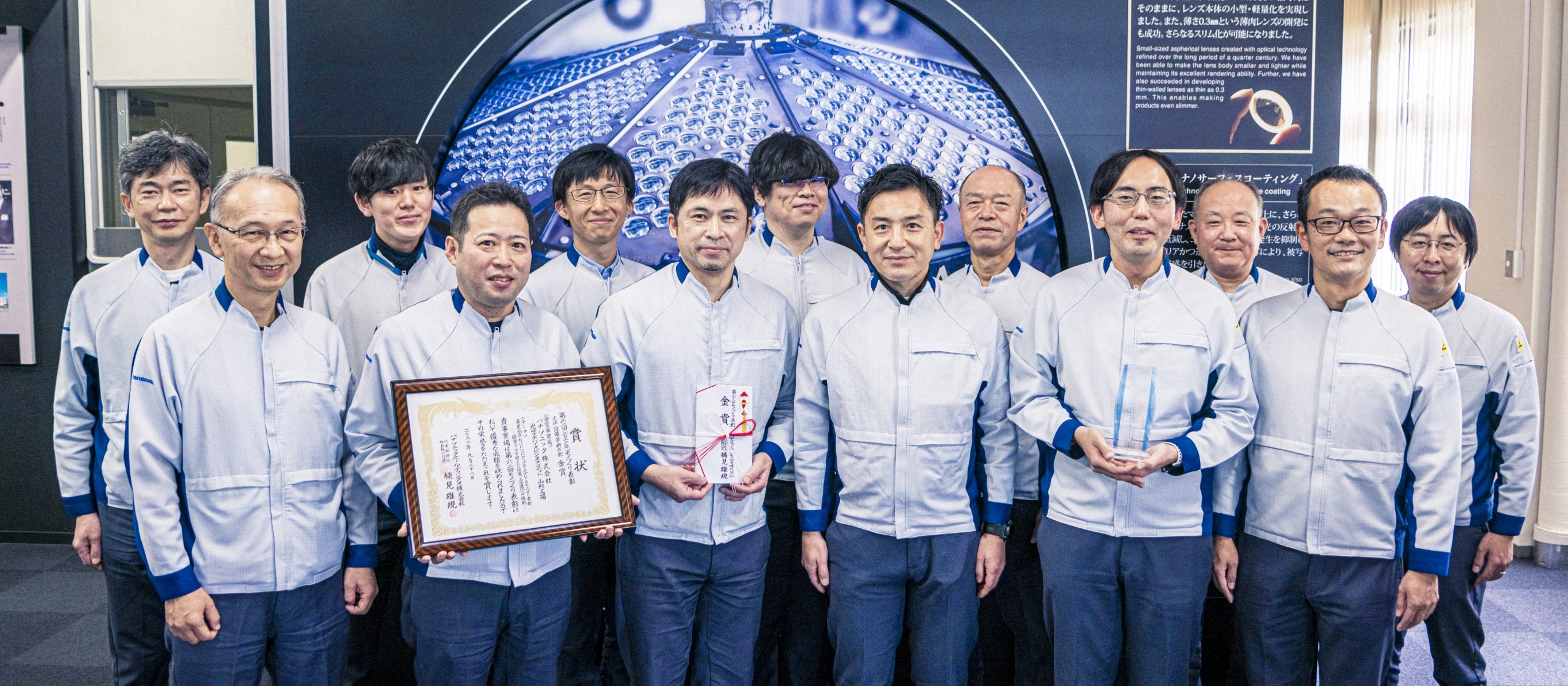
パナソニックグループの全工場を対象に、業務効率や生産性向上を実現し、優れた実績を上げた製造現場に贈られるモノづくり表彰。工法・生産設備の技術革新により経営成果を実現した事例に授与されます。今回選出されたのは、パナソニック株式会社 光学デバイスビジネスユニット 山形工場。
車のフロントガラスに運行情報などを表示するヘッドアップディスプレイ(HUD)は、今や高級車のみならず一般車両にも普及し、需要が伸び続けています。山形工場は2015年からHUD用ミラーの製造を始め、販売数を拡大してきました。しかし、需要拡大による増産要請、高画質化・大型化に伴う加工難易度の上昇、さらに他社との競争が激化し、生産性・加工精度の向上、製造コストの低減が喫緊の課題となっていました。山形工場は製造工程を刷新し、従来よりも高い要求値にもかかわらず劇的に合理化を可能とする新たな自由曲面成形工法を開発。生産性を大幅に向上する改良を実現し、HUD業界シェア率トップ3の実現に貢献しました。高品質、高精度が欠かせない車載機器とそのモノづくり。今回の設備革新で中心的な役割を果たしたメンバーに話を聞きました。
プロフィール
-
清野 文寛
パナソニック株式会社 光学デバイスビジネスユニット 設計開発
-
初田 裕貴
パナソニック株式会社 光学デバイスビジネスユニット 設計開発
-
沢田 亮人
パナソニック株式会社 光学デバイスビジネスユニット 設計開発
-
古市 雅之
パナソニック株式会社 光学デバイスビジネスユニット 生産技術
目次
パナソニック株式会社 光学デバイスビジネスユニット 山形工場とは
1982年に操業を開始した山形工場は、ビデオのヘッドシリンダーから始まり、ムービー用の鏡筒と非球面レンズを製造。中でも、デジタルカメラ用レンズでは、数々のモデルでコアとなるパーツを製造してきました。しかし、デジタルカメラ市場が縮小傾向となった背景から、山形工場は車載機器のBtoBへと事業を拡大。2015年から車のバックモニター用カメラの製造がスタートしました。同工場は光学技術を生かしたHUD用のミラー製造にも挑戦。安定した生産手法を確立して、さらにその生産力を高めています。
5年後の需要拡大を見据える 最優先課題は、大幅な生産性向上
HUDの工法革新にいたるきっかけを教えてください。
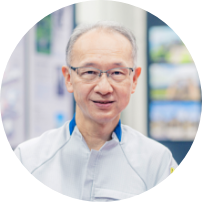
パナソニック株式会社はHUDメーカーとしては後発で、2017年時点ではシェア圏外でした。しかし、2019年の予測でも需要は着実な伸びを見せており2024年に6倍の販売数が見込まれるほどでした。そこで課題に上がってきたのが、いかに生産数を確保するか。また、市場では高画質・大画面の製品が求められ、より高精度の加工が必要になる一方で、競合メーカーによるHUD用のミラーの低価格化が続き、大胆な生産コスト削減が必要でした。
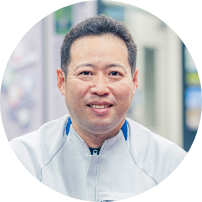
大幅な生産効率向上とコスト削減は、製造工程全体で工法を改良しなければ、成し遂げられません。そこで、ミラー材料の見直し、成型、成膜の3工程が一体となった工法改善に2018年頃から本格的に着手しました。
具体的な工法の革新内容について教えてください。
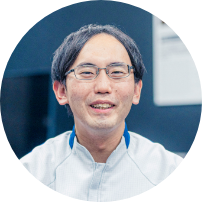
成型工程では、金型補正ソフトの改良に着手。これまで補正ソフトは私たち成型担当者には扱いが難しく、他部署に補正をお願いしていました。そこで、自分たちで金型を補正できるようにとコンセプトを決めました。ソフト設計は初めての経験でしたが、光学設計の担当者に協力をいただき、自由曲面に対応したプログラムを完成させました。中身は複雑でも扱いは非常に簡単なのが特長で、高度な数学の知識がなくても高精度な金型補正が可能になりました。
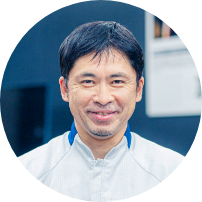
材料は、高価な光学材料から安価で入手しやすい汎用材料への切り替えに挑戦。品質問題もクリアしつつ、材料コストを大幅に抑えることに成功しました。
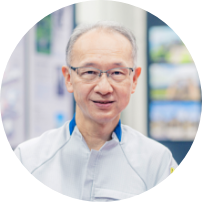
成膜工程では、新工法の採用を検討し続ける中で、展示会に出掛けた上司から光学部品外の成膜装置を勧められました。メーカーで確認すると、今まで時間が掛かっていた成膜工程をわずか数分へと短縮する高スピードの装置でした。装置自体は小型でしたが、大型化すれば生産性10倍以上に手が届くと確信しました。そのメーカーで光学部品に使用した例はなかったのですが「ぜひ、一緒にやりましょう」と力強く応えていただき、二人三脚で工法開発に取り組みました。新成膜工法に関してわれわれは素人でしたから、メーカーに大型化を検討してもらう際には、ずいぶんと見当違いなことを言って困らせてしまったかもしれません。しかし、非常に頑張っていただいて、成膜装置の完成にこぎつけました。1台でこれまでの装置10台分以上の働きをしてくれる頼もしい存在です。
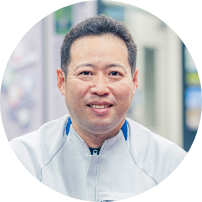
沢田さんたち設計技術部が開発した工法を、実際の製造過程に落とし込んで量産体制を確立するのが、私たち生産技術課の仕事です。新成膜工程は自動化されていましたが、その前後の工程、例えば製品の投入や事前処理、装置からの取り外しなどの工程には7人が必要でした。工場は24時間稼働、1日で最低21人の人員を確保しなければなりません。そのうえ、前後の工程は非常に繊細かつ負担の大きな作業となり、成膜の品質は作業者に依存していました。
これでは高効率な新成膜工法を十分に生かしきれないと、成膜の製造フローの完全自動化に踏み切り、沢田さんたち設計技術部と一緒に検証しました。
検討を進める中で秒単位の制約条件などが出てきました。その自動化に苦労しましたが、議論とテストを重ねて安定した品質、生産数を確保することができました。HUDミラー製造のモノづくり革新により、材料コストを大幅低減、成型精度は4倍近くまで飛躍的に高めました。さらに、成膜工程における生産性でHUDにおけるパナソニック株式会社のシェア率向上に寄与できたと考えています。
HUD以外の製品に広げたい 山形工場ならではの自由曲面加工
初田 裕貴 [設計開発]
金型補正のソフトウエア開発については、他部署の光学設計の力を借りて多くの知見を集めて何とか成立したと考えています。さらに、現場のみなさんに知恵や力、そして設備や評価機器まで貸していただき、金型補正データの精度を大きく高められました。金型の温度分布改善を含めた今回の取り組みは、さまざまな工程を合わせて一体化で進めてきたので、お互いを補完する形で助けあえたことが大きな成果につながったと思います。
実はHUDミラー以外の製品もどんどんと複雑化するトレンドがあります。今回開発した技術は、レンズや他の光学部品にも応用できる技術ですので、開発したソフトウエアで山形工場全体のモノづくりの技術力底上げに貢献できればと思っています。他の自由曲面が必要な製品にも落とし込んでいくことで、より社会の要望に応えられるような新たな製品を生み出していきたいと考えています。
材料刷新で実現したコストダウン 支えたのは社内外の知恵
清野 文寛 [設計開発]
材料は成型や成膜といった後工程の全てに影響してくるので、そこへの影響も考えながら開発を続けます。プロジェクトメンバー始め、上司や周囲の仲間たちのサポートがあって、汎用材料への切り替えが実現できたと思っています。また、材料メーカーに協力いただけたことも非常に大きかったですね。打ち合わせで、市場で同様の課題がないかなど多くの知見をいただき、分析にも力を貸してもらいました。社内外の知恵を結集してするコミュニケーションの重要性に改めて気付かされました。
成膜機メーカーと共同で挑んだ 高効率追求型の新成膜工法
沢田 亮人 [設計開発]
HUDを搭載する乗用車の内部は、特に夏場は非常に高温になる大変過酷な環境です。光学専用の部材から、汎用材料へと変更したことで、高温環境では成膜面が浮いたりはがれたりする現象が出て、なかなか解消できませんでした。そこで成膜機メーカーとアイデアを出し合って何度もトライし、新たな事前処理を施すことで膜の密着性が向上しました。
今回は成膜機メーカーに多大な協力いただいて、生産性向上を達成できたと思っています。色々なところに出て行って、色々な情報を得る、色々な人と会う――。自分たちの領域に落ち着くのではなく、協力関係を構築できると、スムーズに仕事が進みイノベーションにつながると実感しています。
HUDのさらなる普及へ 生産技術の歩みを止めない
古市 雅之 [生産技術]
今回、皆の衆知を集めて具現化したシステムは、われわれが独自に蓄積してきた「ノウハウ」や「固有技術」に新たな要素を加えて実現した世の中にないもので、他社が容易にマネできない生産技術要素です。そこに満足することなく、保有する「他社に無い強い商品、技術」の優位性を活かしつつ、技術・モノづくり革新に挑戦する風土構築をリーダーとして推進し、モノづくりの進化・深化にチャレンジして参ります。
また、生産技術者として、単に製品開発品を量産フェーズに移行させて安定生産を目指すだけではなく、製品の企画開発から販売に至る一連の流れに積極的に関わる必要があると感じています。顧客要望の高度化などに備えた先行生産技術の開発、デジタル技術導入による管理法の最適化や最適生産化を推し進め、生産プロセスの多重化や複雑化に対応した生産技術力を向上させていきます。
今後、ヒューマン・マシン・インターフェースのベースになるHUDの重要性はより一層高まる中で、われわれのモノづくり技術を更に進化させて商品力を向上することで、HUDの普及率を上げ、ドライバーや歩行者の安全確保に貢献していきます。われわれの使命は、お客様が新たな商品を創出できるような光学デバイスを提供し続けることを通じて、世界中の暮らしのアップデートを具現化することだと考えています。われわれの技術を進化させ続けて、よりよい社会と継続的な事業成長を実現いたします。
受賞テーマ | 事業成長へ向けたヘッドアップディスプレイのモノづくり革新 |
---|---|
担当 | パナソニック株式会社 光学デバイスビジネスユニット 山形工場 |
*所属・内容等は取材当時(2023年2月)のものです。
HUDはダッシュボード下に設置されたユニットからナビの情報やスピード情報をフロントガラスに投影して、ドライバーの負担軽減や車の安心安全をサポートする機器です。HUDユニットを構成するのは、情報を映写する表示機と映像を反射させてフロントガラスに届けるHUDミラー。ここに生かされているのが、非球面レンズや交換レンズをつくってきた光学デバイス技術です。